SCL is a strong player in Carbon Black and has executed big projects at all the major Indian Carbon Black manufacturing facilities. SCL manufactures the complete range of quality refractory for the hot face and the backup layers of tread and carcass reactors.
SCL makes single large precast shapes like Ventury and Tangential air inlets blocks with its exclusive capability, thereby considerably reducing number of joints. Addition of Alumina-Zircon and Alumina-Chrome refractory for the hot face is testimony to our commitment.
Realising that design plays a major role for the performance of refractory, SCL offers complete refractory and backline design on the basis of heat calculations, ease of installation and various operating parameters.
In addition to providing refractory lining designs and materials, SCL also offers full technical backup for analysing and solving problems.
The refractory required for Carbon Black Reactors are subjected to severe conditions ranging from extremely high temperatures up to 1900 0C, severe abrasion to thermal shock during use.
We at SCL realise the impact of these factors and we exercise rigorous control over our manufacturing and inspection procedures to ensure that all our refractory parts meet these critical criteria. Some measures that we have taken to ensure this are:
- We have developed a unique bonding system which does not produce any liquid or glassy phase even at elevated temperatures.
- We have developed a computer-aided model for particle size distribution to improve various properties of the refractory.
- We use advanced vibro-casting technique to manufacture large and complicated precast single shapes.
- All refractory bricks and shapes for carbon black reactors are assembled and marked at our plant, before dispatch. This ensures dimensional accuracy and ease of application at customer’s end
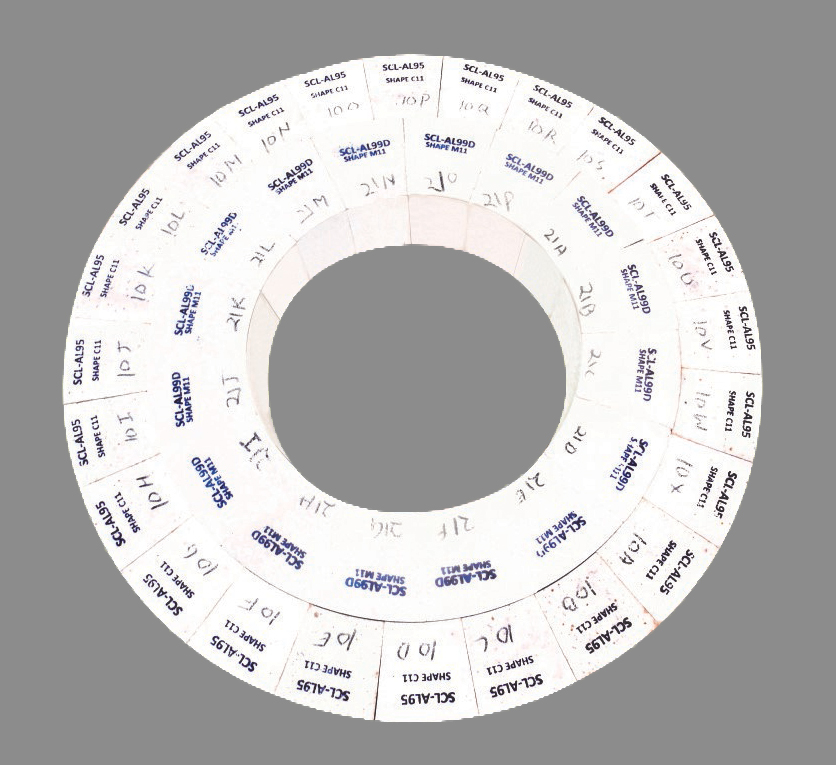
An assembly for Carbon Black reactor
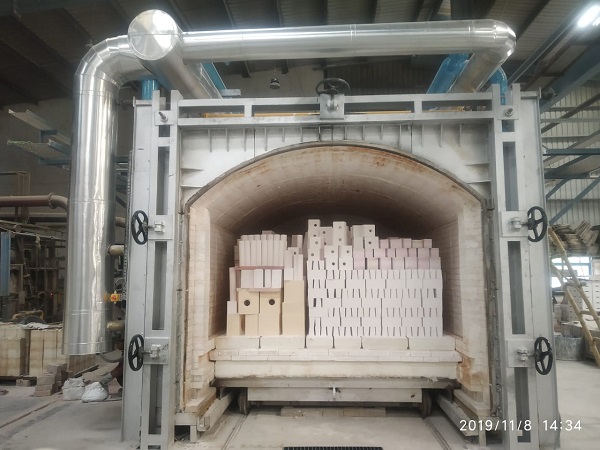
German Kiln for firing temperatures up to 18000 C
Here is our range of refractory for Carbon Black: